Double-Wide Blanket
- marymjones12
- Feb 6, 2023
- 3 min read
Last fall, my cousin commissioned me to weave a blanket for her son who is in college studying architecture, and who had recently moved into his first off-campus apartment. Having just tech-edited a gorgeous double-wide blanket for WEBS (the "Ebb & Flow Double-Wide Chenille Throw" by Wendy Bestor), I knew I had a great jumping-off point for making a giant blanket with an amazing hand.

My cousin helped greatly in deciding on colors to match her son's decorations and stylish sensibilities (I find color is often the hardest decision in the whole weaving venture!) I veered off the official pattern by creating my own stripe sequences -opting for something that was more symmetrical and played off of numbers in the Fibonacci sequence.

One of the tricks in weaving double-wide is making the middle seam as inconspicuous as possible, which usually involves some finagling at the selvedge fold.
One way to do this is to widen the sett at the turn. Following the pattern, I sleyed the left selvedge at the join at half of the double-wide sett for the last half-inch (4 dents) of the reed - so at 16 epi (2 ends per dent in an 8-dent reed) instead of the regular 32 epi (4 ends per dent).
Following the suggestion of my Master Weaver instructor, I also added a supplementary stand of 3/2 cotton in each of these 4 dents that I weighed off the back of the loom with empty yarn cones. I threaded each supplementary strand on the same shaft as the leftmost thread in each of these dents (in its own heddle) so they imitated what the leftmost warp ends were doing in the cloth. The added 3/2 ends mimicked the bulk of the rest of the piece during weaving, but with the intension of them being removed once the piece was off the loom.

Using the contrasting 3/2 cotton ends as a visual guide, while weaving I noticed that the two leftmost warp ends turned under at the fold.

About three fourths of the way through weaving, I realized that I must have a threading error my bottom-most layer of cloth that caused a three threads to mimic each other. It was only noticeable on the underside of the weaving, which was the bottom layer of the fabric. At this point in the project, I decided to keep weaving on as I had been and to correct the error by hand off-loom.
As usual, I had built in some extra space in the warp to verify I had everything set up correctly, sample my beat and experiment with different shuttles before starting the blanket itself. But since this threading error affected only the bottom layer of the cloth on the loom, I didn't catch it until I had woven enough to start building up fabric on the cloth beam. In the future, I think I am going to budget in enough extra warp to cut off my standard ~12" pre-project sample to make sure all layers and sides of the fabric are set up correctly when I am weaving double-wide.
Fortunately, this error was a relatively easy to mend. Once the web was cut from the loom (and before it was wet finished) I carefully extracted the errant thread while attentively hand-sewing in its replacement in the correct over-under orientation. I would slowly pull out a ~1-2" of the mistaken warp end and then sew up to the transition point with a long replacement thread. To match the tension on the rest of the blanket, I had to pull, stretch and bend the cloth as I sewed in the new thread so it was pliant and not rigid. This was quite a workout on such a big piece!
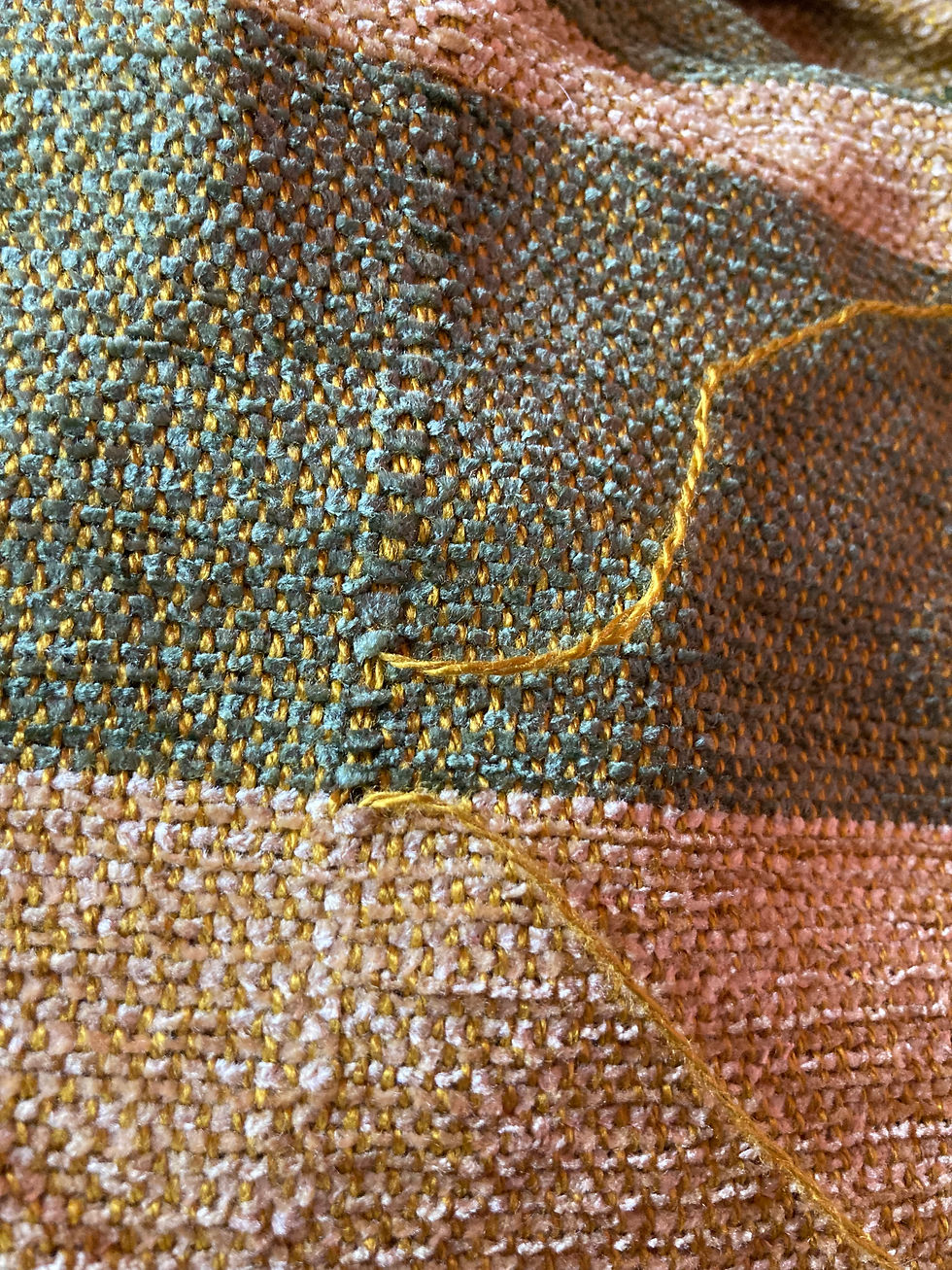
Again, it was great to have a sample to practice fixing the error on before committing to the final piece. It was slow-going but the benefit of such a simple weave structure is that I was confident I was sewing in the replacement warp end in the correct sequence.
I also carefully extracted the 3/2 cotton supplementary warp ends at the turn before wet finishing in the washer and dryer.
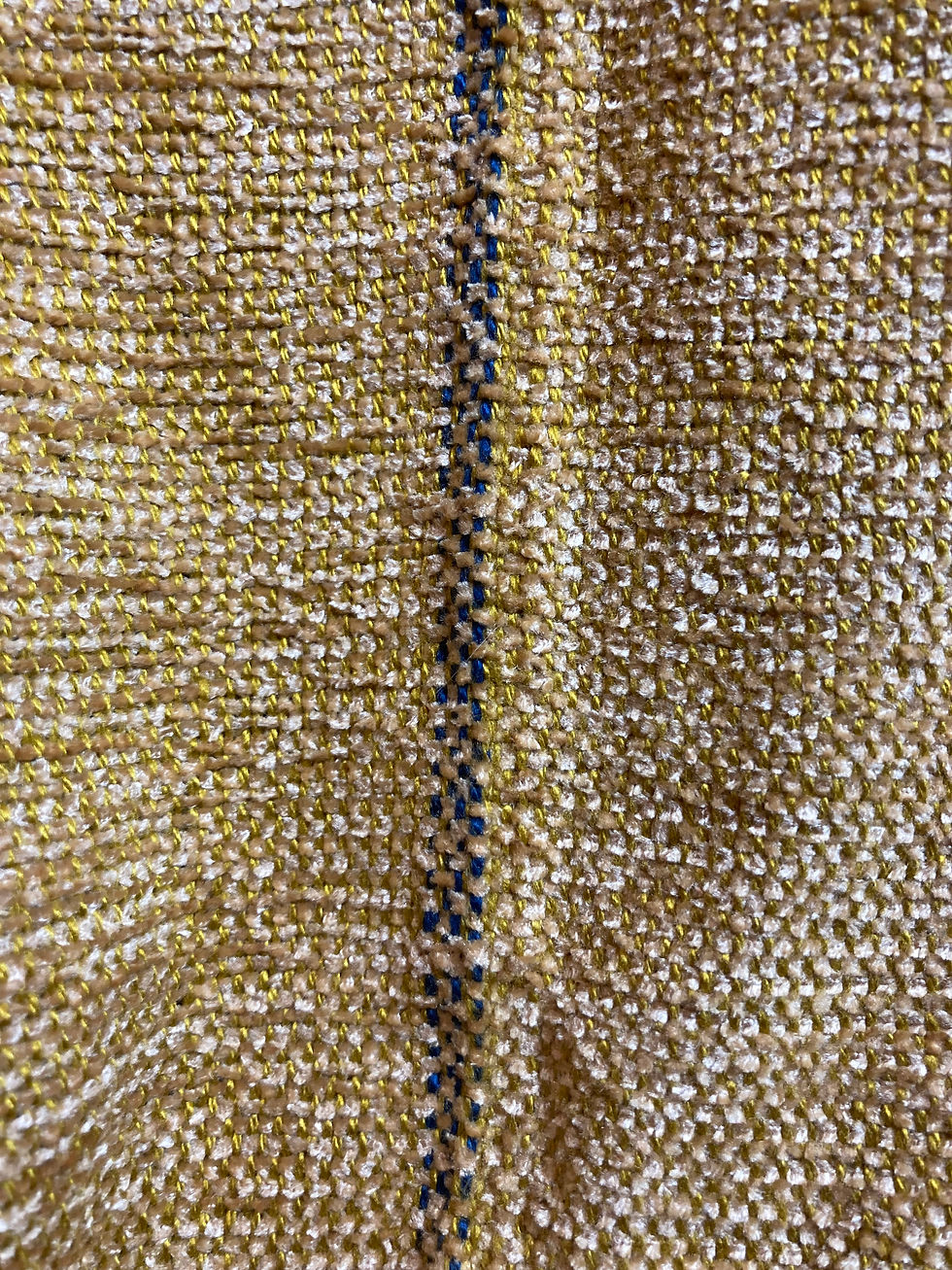
The turn was hardly visible once it has been wet-finished. You can barely see it in the image below running vertically down the center of the blanket.

Are more double-wide blankets in my weaving future?? Absolutely!
Comments